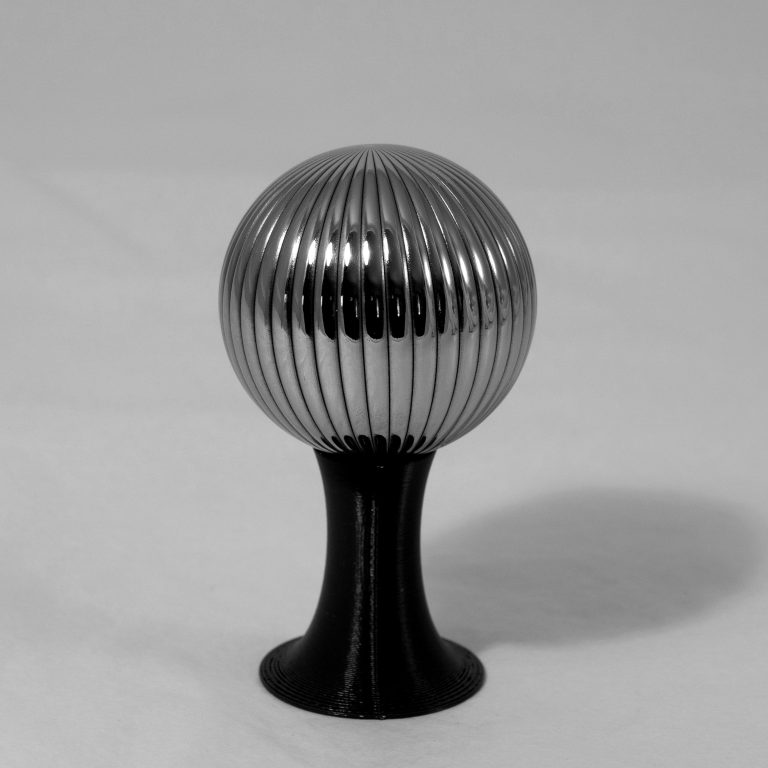
Changing the aesthetics by adding a design
5-axis laser texturing is a specialised manufacturing process that involves the use of lasers to create complex and precise textures or patterns on the surface of three-dimensional objects. Unlike traditional methods which are limited in their ability to achieve complex designs, laser texturing is a precise, repeatable process with limitless design possibilities.
How is this method different?
In 5-axis laser texturing the term “5-axis” refers to the multidirectional movement capabilities of the laser system used for the texturing process. What stands this method out is that the texturing equipment can move the laser head in five different directions. This additional freedom of movement allows the laser to access and texture complex three-dimensional surfaces from multiple angles including curved and contoured surfaces.
Where is this method utilised?
Due to its ability to create precise and customised surface textures on a wide range of materials the applications of 5-axis laser texturing are continually expanding. This technology is particularly popular with toolmakers due to its ability to texture moulds, dies, inserts and other tooling components with intricate patterns and textures. This enhances their grip, wear resistance and functionality. In the plastic moulding industry textured moulds ensure better part ejection, reduced friction and improved surface finish of moulded parts. For stamping and forming dies laser texturing helps in reducing material adhesion, minimising tool wear and prolonging tool life. Toolmakers also utilise 5-axis laser texturing for creating custom textures that facilitate better lubrication and heat dissipation leading to improved manufacturing efficiency and product quality. By incorporating 5-axis laser texturing into their toolmaking processes toolmakers can achieve higher precision, increased productivity and superior performance in their tooling applications.
Mould texturing can also be used to elevate the aesthetics of a component by putting a design into its surface. For example, a wood grain effect in window mouldings or a leather effect on car dashboard components.
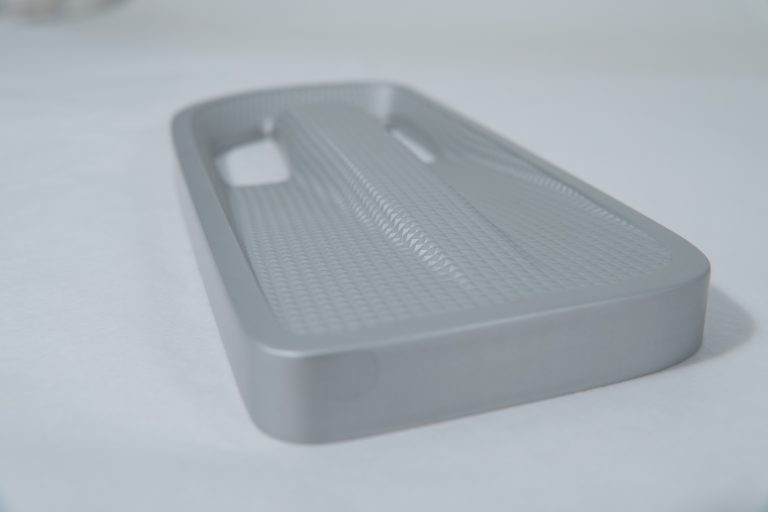
How is the texture design achieved?
Intricate patterns and textures are achieved through precise manipulation of a high-powered laser beam across the surface of a material. This process involves the use of Computer-Aided Design (CAD) software to design the desired texture or pattern by specifying details such as depth, shape, and orientation. Once a texture or pattern is programmed into the CAD software and applied to one tooling component it can be effortlessly replicated across other components with precision and consistency.
What are the benefits over other methods?
This method offers several benefits including greater precision, reduced tool wear (because there is no physical contact), faster production times and the ability to create consistent intricate details. Whether it’s creating fine features on moulds or applying intricate textures for improved release, this technology offers flexibility to meet diverse requirements and ease of replication. As a result the manufacturing process is streamlined, lead times are reduced and overall production efficiency for toolmakers is enhanced across various industries. Additionally, being a digital process designs can be easily rescaled or faded out at the edges of tools to reduce scuffing during mould release.
If you are looking to explore the benefits of 5-axis laser texturing and its potential applications for your manufacturing needs then get in touch with Fimark. Our team of experts is ready to discuss how this technology can enhance your operations and help you achieve your production goals.